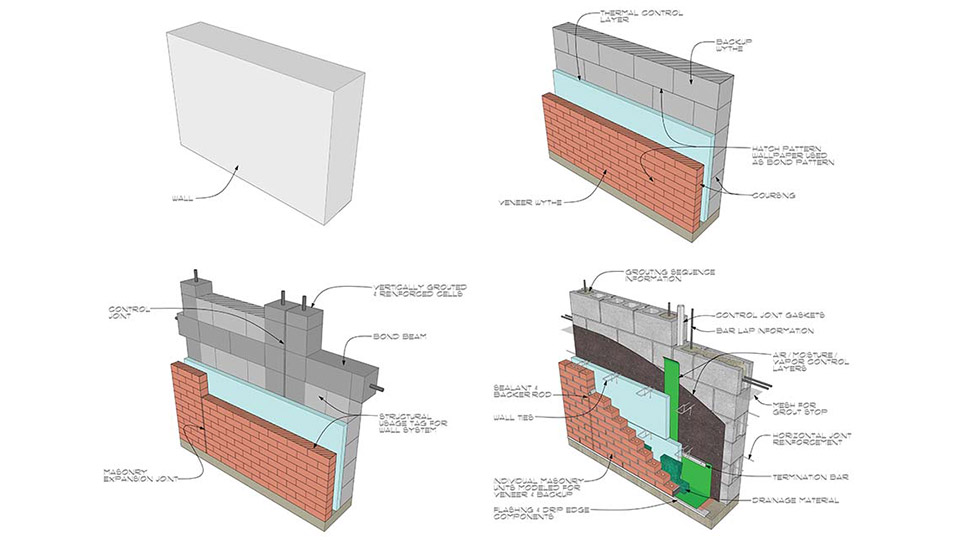
Figure 1: Masonry cavity walls, at various levels of development (LODs), have been incorporated into the 2014 LOD Specification by the BIMForum.
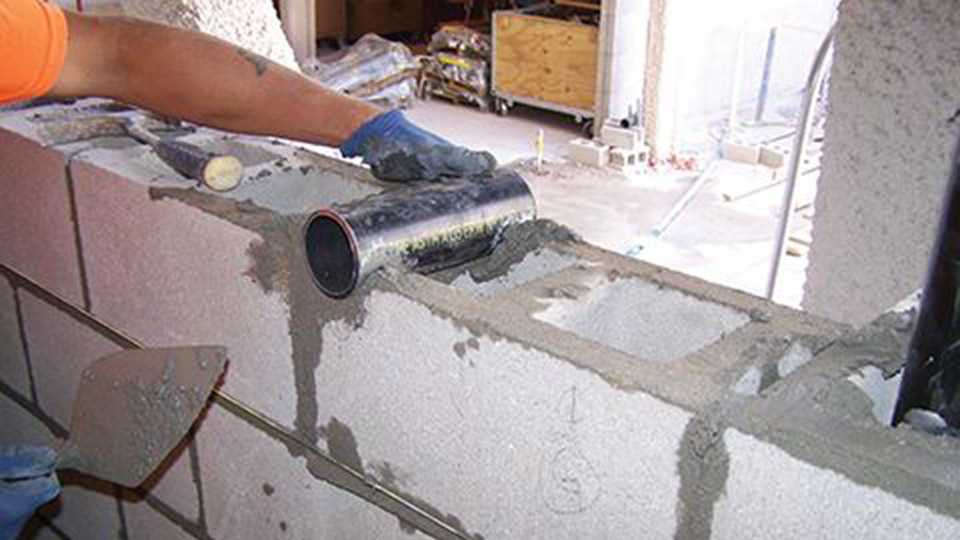
For this project, the bricklayers worked alongside the mechanical, electrical, and plumbing (MEP) trades to install pipe sleeves through the masonry walls as they were constructed, per the BIM model.
The increasing sophistication of BIM models gives masonry subcontractors the opportunity to provide project information much earlier in the planning. Without BIM, a mason contractor rarely has the information needed to fit masonry tasks within the overall schedule or sequence of trades. With this limitation, a schedule is simply durations of tasks or walls based on typical crew sizes and assumptions about site access. With BIM-M, mason contractors can see how their tasks fit within the master schedule, which enables them to make more accurate predictions about task duration and labor needs.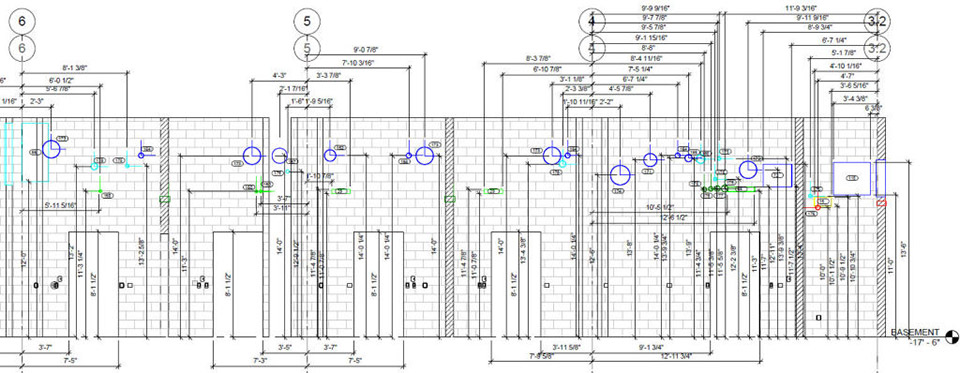
This partial elevation view of the composite model locates the MEP sleeve penetrations for the bricklayers. Each sleeve has a unique number and is color-coded per trade, as outlined in the caption to Figure 2.
The symposium’s ‘contractors’ session had several highlights. IMI’s Mark Swanson presented an overview of BIM and digital technologies expanding throughout the construction industry. Jim Schrader of Power Construction (Chicago) gave the general contractor perspective on what BIM services masonry contractors need to provide as part of the overall project–a model that can be useful with clash detection is essential. Adrian Siverson of R&D Masonry (Marysville, Washington) and Peter Sindic of Richards & Weyer Construction (Lyons, Illinois) gave two perspectives of BIM services masonry contractors are doing on projects. The mason contractors found efficiencies and economy from using some level of BIM on projects, even when they are not mandated to use it on the overall project.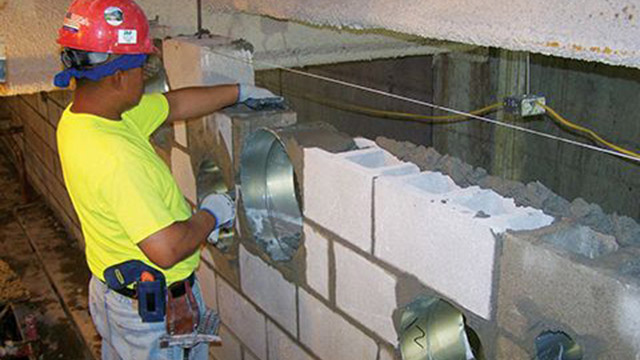
In the photo above, a bricklayer installs mechanical duct sleeves at precise locations per the BIM model, as he constructs the masonry.
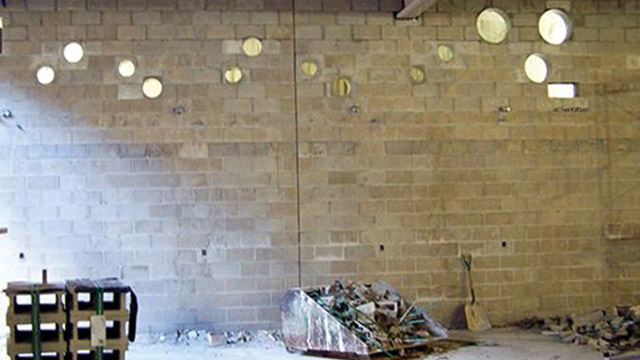
As the concrete masonry wall was constructed, the bricklayers installed 468 sleeves for fire protection, 231 sleeves for plumbing, 343 sleeves for water, and 10 miscellaneous sleeves. There was a total of 1537 sleeves.
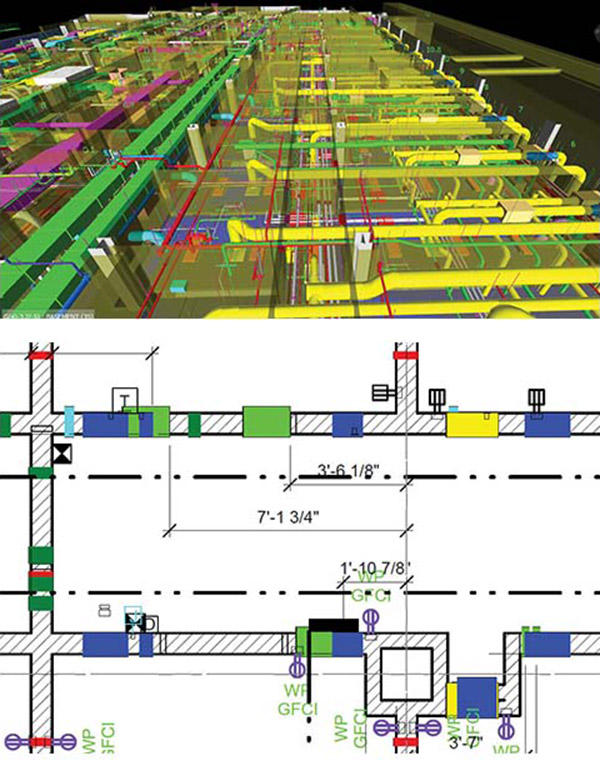
Figure 2: The coordination model in the top image shows MEP pipes and ducts passing through the masonry walls. In the lower image, a plan view of the composite model shows some of the MEP penetrations. Light green is mechanical, dark green is water, yellow is electrical, red is fire protection, blue is HVAC, and cyan is plumbing/domestic water vent.
As a result, the masonry on this project progressed in coordination with other trades, rather than in opposition–an obvious benefit to both the contractor and craftworkers. It also provided the opportunity to showcase the benefits of designing and constructing with masonry to the owner, designer, and construction manager/general contractor.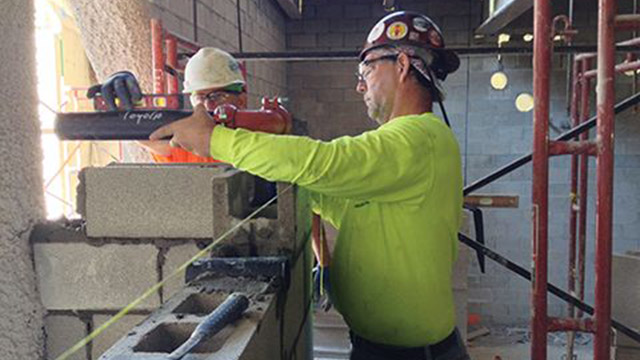
A bricklayer (left) works in alongside a pipefitter (right) to simultaneously construct the block wall and the plumbing contained within it.
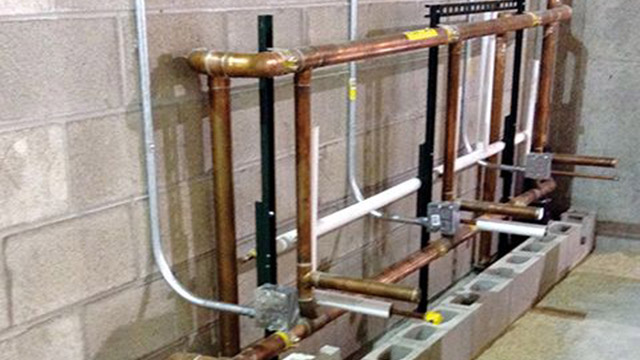
The BIM model made it possible to prefabricate the toilet room plumbing assemblies on steel strut racks to conserve space onsite. The plumbing racks were integrated into the block walls per the coordination model.
Weekly job meetings run by the masonry foreman were critical. The MEP trades needed to know the masons’ plans four to five days in advance in order to relocate their manpower from other areas on the job, and to stage their horizontal penetration sleeves and vertical in-wall piping, making sure to have them ready for the masons at the proper time. Each day (sometimes twice daily), the mechanical and plumbing foremen checked in with the masonry foreman on specific labor and material needs.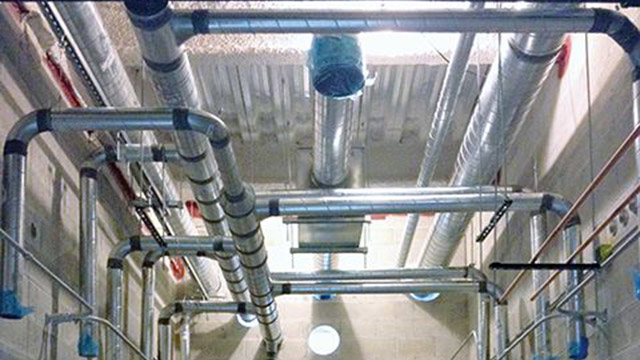
Upon completion of the masonry work, the MEP trades were able to easily install their pipes and ducts without cutting through the masonry due to the well-coordinated sleeve penetrations.