Raising The Line
Words: Paul BenderWords and Photos: Paul Bender, Inside Sales Coordinator at Bon Tool Co.
The connection between the human hand and tools is both innate and learned. Immanuel Kant is quoted as saying the hand is the visible part of the brain. As a link between the two, efficiency is vital in the modern-day workplace especially as it relates to production and hand tools. One great breakthrough in hand tool efficiencies laid the foundation for Bon Tool Co, the Corner Pole.
Corner Poles or Masonry Guides, as noted by Richard T. Kreh, Sr, are engineered from a high-grade aluminum and are sold in sets where the fittings and attachments make them useable on a number of different setups. Including chimneys, elevator shafts, inside corners, outside corners, and quoin corners. They can be adjusted to varying heights and also used in other types of masonry work. The corner pole when set up correctly is a constant that is both vertically plumb and horizontally level at the base point, which is well described in ‘Masonry Skills’ written by Richard T Kreh.
Once the corner pole is set up and secured properly, it serves the same function as a masonry corner or lead, and it takes significantly less labor to build a brick corner. The corner pole when set up correctly is constantly being vertically plumb and horizontally level at the base point, which is well described in the Masonry Skills textbook written by Richard T. Kreh.
R model corner poles (11-487) are unmarked and used mainly in veneer work, and ‘Model C’ (11-165) are poles that are marked with scales, including standard brick and modular scales. Kreh also notes that “Masonry contractors maintain production figures for their masons and estimate using these masonry guides or corner poles increases the daily production by a minimum of 25%”.
Next-generation systems have been developed to build on this innovation. The Continuous Corner Pole System (21-292) is also now available, which exemplifies modern-day advancement.
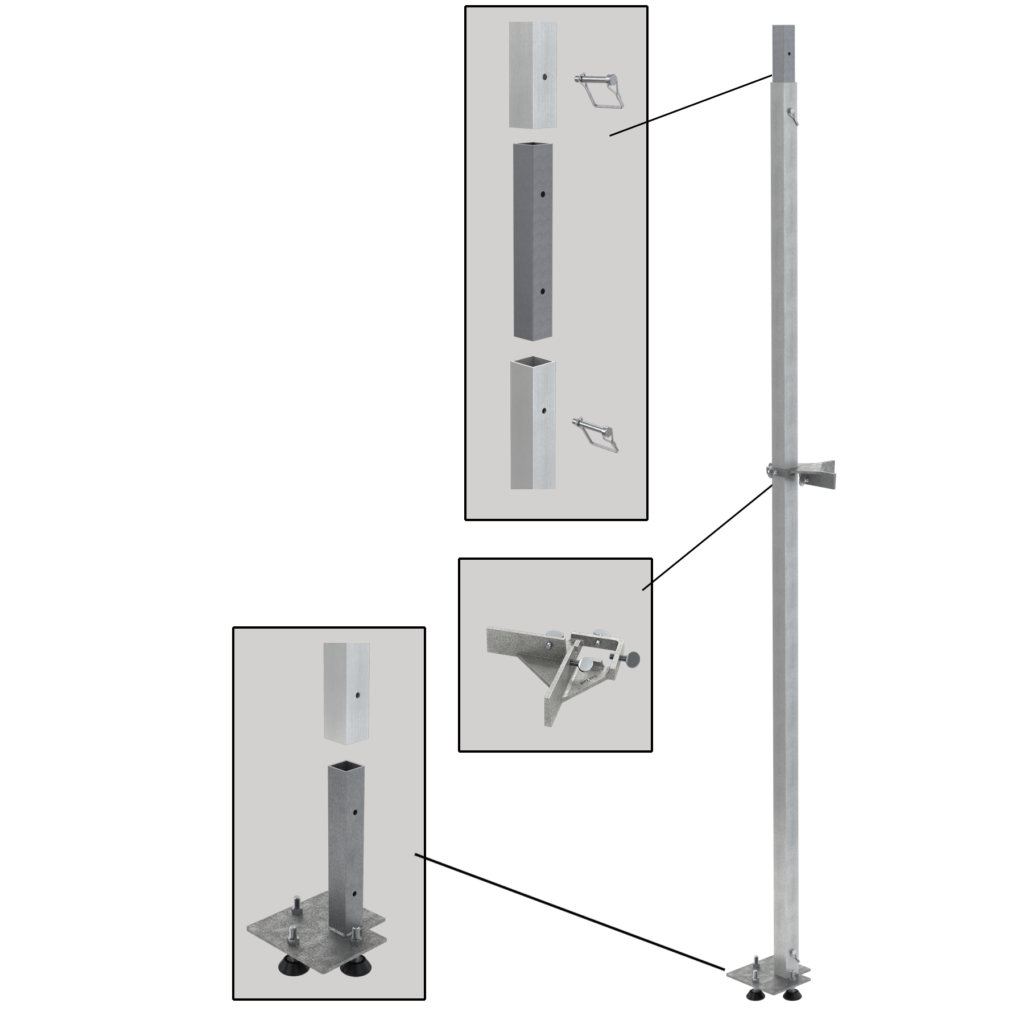
Developed in the field, this system has no height limitation where the contractor can add poles to raise the system to a higher location. This system becomes limitless and is ideal for block work in high spaces like multistory buildings and elevator shafts.
Enabling the contractor to raise the line up another course through this system becomes a much easier task due to the innovation of this masonry guide. Not only does it make this process more efficient but it also improves the quality of work and generates more profits for the contractor. These systems both eliminate the need for a mason to start hours before the crew building a corner.
Reflecting that hand tools can be guided by usage, maintenance, and also in the field modifications – these systems have adapted with time. Linking the brain and the hand to production has been a driving force of innovation for many hand tool manufacturers today. The Corner Pole system and Continuous Corner Pole System raised the line of efficiency and production enabling contractors to produce more effectively than ever before.
SPLIT FROM THE REST:
While traditional power tools are what a lot of consumers are after and usually the sexy option, there is still something to be said about hand tools and equipment that are non-powered that can do similar work without experiencing costly front and back end issues. In the early 2000s, Bon Tool Co started a collaborative effort to streamline the design and functionality of our current splitter offering.
Planning to cut bricks and pavers without hydraulics or power? Our Paver & Brick Buster (11-590) pictured to the left would be our current model and offering. How about cutting/splitting pavers as well as retaining wall units and blocks? Our Block Buster (11-543), pictured to the right, is designed just for that. Both units are non-powered, non-hydraulic, and all mechanical in use. These units have gained popularity as they have less issues on the front and back end of use. Both the Paver & Brick Buster and Block Buster have tri-cut replacement blades that, in essence, triples the blade life. Surprisingly portable, low-noise, low-dust, and are respectively light-weight (11-590 = 47 lbs , 11-543 = 137 lbs) are some other advantages over traditional powered equipment options.
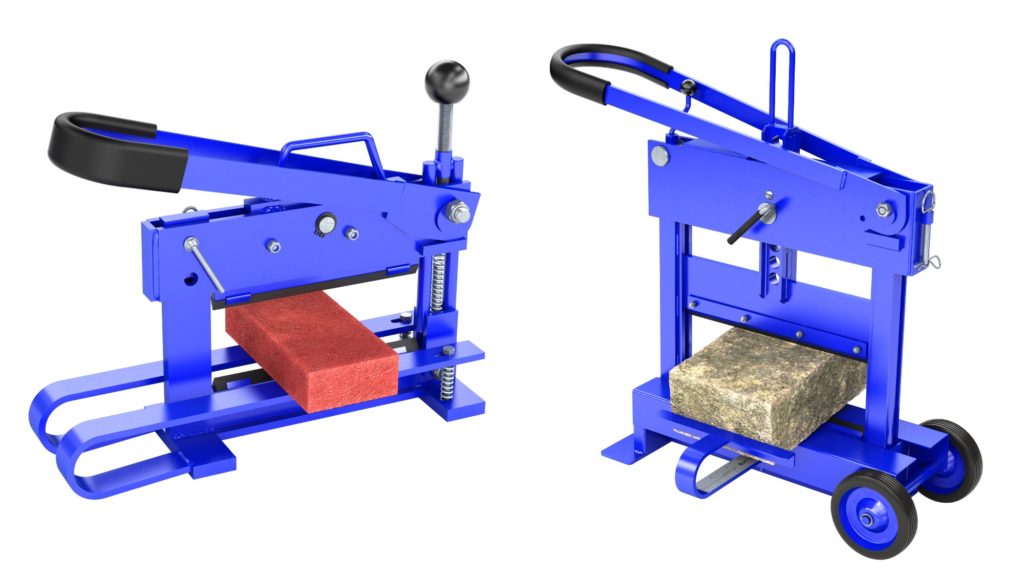
Leveraging for work has become easier with these units as they both can be easily incorporated into job costs. After an initial job or two, their value becomes more evident. All things considered: having a non-powered yet efficient option in splitting is becoming ever more valuable in today’s market. Not only is this a better option for the environment (limited dust/no fossil fuels), but it also benefits the pocket as it is much more cost-effective than other alternative options on the market today.
Initiating a closer look at the Paver & Brick Buster (11-590), this unit’s cutting blade is 10 inches wide, and the height of the unit can be adjusted with a 3-position removable pin with a cut depth of 3 3/8 inches and an adjustment screw at the top for fine adjustments. The Block Buster’s (11-543) cutting blade is 16 1/8 inches wide, and the cutting depth is anywhere between 1 inch and 12 inches. The handle locks in place for easy moving (on wheels) at and around the jobsite.
These splitters both function similarly in use. To adjust initially to the block or brick size, use the pull pins on either unit. Then once close to the cutting surface, use the fine-tune adjustment pins on the top of either splitter to have the blade meet the block or brick and the handle elevated at a 45o angle. Next pulling the handle puts the pressure on the base of these units and gives a natural split on either block, brick, and/or pavers. These units both provide a simple and rugged design and still maintain as fully functional and portable. While the mechanical nature and triangular blade limit front and back end maintenance, these units are also cost-effective options to saw cut (diamond blades) and other powered equipment options which tend to be higher in price. Finding a good blend between non-powered equipment and powered equipment/hand tools is the responsibility of the contractor. Understanding that the sexy option isn’t the only option splits these units from the rest.